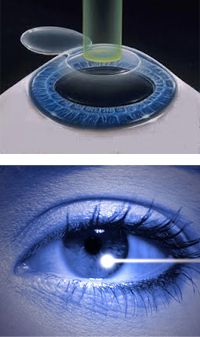
An existing customer in the medical industry commissioned Syntec Optics to mold the second generation of components for their eye surgery kit, which consisted of 3 molded polystyrene lenses and 1 molded polycarbonate opaque part. Syntec Optics forged a solid relationship with the customer by successfully molding the first generation of parts for years while offering invaluable technical support throughout the life of the program. Therefore, the customer had good reason to trust us with the launch of their new product line.
Upon reviewing the customer’s drawings and CAD models, we were able to utilize our Design For Manufacturing and Assembly (DFMA) skillset to help the customer optimize the geometry of the mating features of two components (one of the lenses and the opaque part) for ease of production and assembly. Our advanced skills, including Single Point Diamond Turning (SPDT) of optical inserts, tool-making, injection molding, and analyzing of molding processes through capability studies, allows Syntec Optics to build and qualify multiple sets of tooling for the new components.
Meeting the new tighter tolerances posed a challenge to qualifying the molds. For example, one of the new lenses had to be molded to the same irregularity tolerance as the first generation lens (4 fringes maximum @ 632.8 nm) but over a working clear aperture that was 40% larger. Several of the mechanical tolerances for the opaque component were also reduced to ± 20 microns. Syntec Optics was able to meet the new tolerances and the customer was extremely pleased with the performance of the entire product line. Years after the launch of the second generation, the customer continues to receive praise from the medical field for the excellent performance of the new components.
For more information on this project, or to learn more about our other products and services, please contact Syntec Optics.